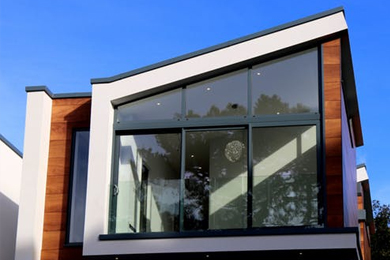
What Is Design-Build Construction ?
Design-Build offers a collaborative and efficient method of completing a construction project that leverages the strengths of single-source planning, design, and construction expertise. Design-Build allows Horst Construction to bring greater levels of accountability, value, and control to your project. Our primary function is to act as our client’s advocate, and we use our significant knowledge to select, negotiate, and hold the entire project team accountable – from designers and engineers to vendors and subcontractors. Combined with our deep knowledge in construction, the Design-Build method enables us to exert greater control on project’s timeline and costs, while providing one trusted point of contact for questions during – or after – construction.
Transparency
As the Design-Builder, we are completely transparent or “open book” about the process, costs, and profits. Together, we agree upon a set fee based upon percentage of construction value, hourly billing rates, and percentage of shared savings. This eliminates the surprises that catch so many owners off guard and provides an honest and communicative framework for the project.
Savings
Design-Build construction costs trend lower than other delivery methods. The Design-Build design and construction schedule can be 23% faster than Construction Management at Risk and 33% faster than General Contracting.
Reduced Risk
With this model, Elbros Group assumes responsibility for risk which is otherwise placed on the project owner, including risks against scope of work, schedule, cost, and quality. We manage the risk while maintaining our high ethical standards of treating all stakeholders fairly.
DESIGN-BUILD PROCESS STEPS
The design-build process can be broken down into five main steps: team selection, project planning, design, GMP/bidding, and construction. For the most part, these steps will happen sequentially, but not necessarily independent of one another. The project planning, design, and bidding phases may overlap. Construction may kick off while some of the project is still in the design phase. Ultimately, it will depend on your specific project and your goals.
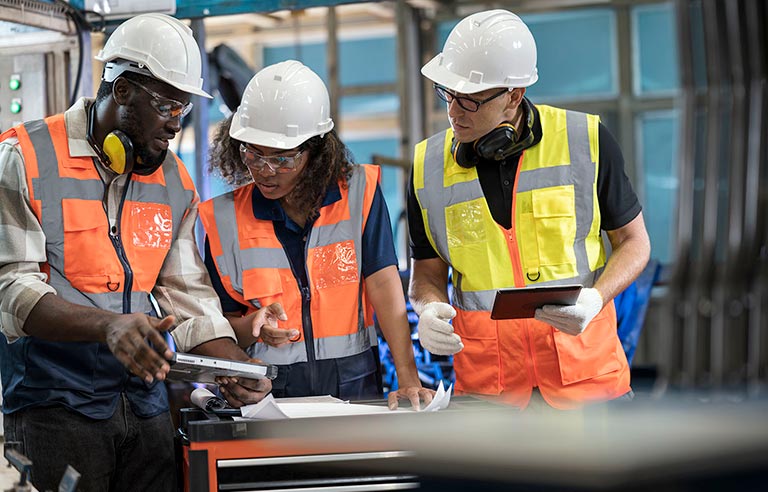
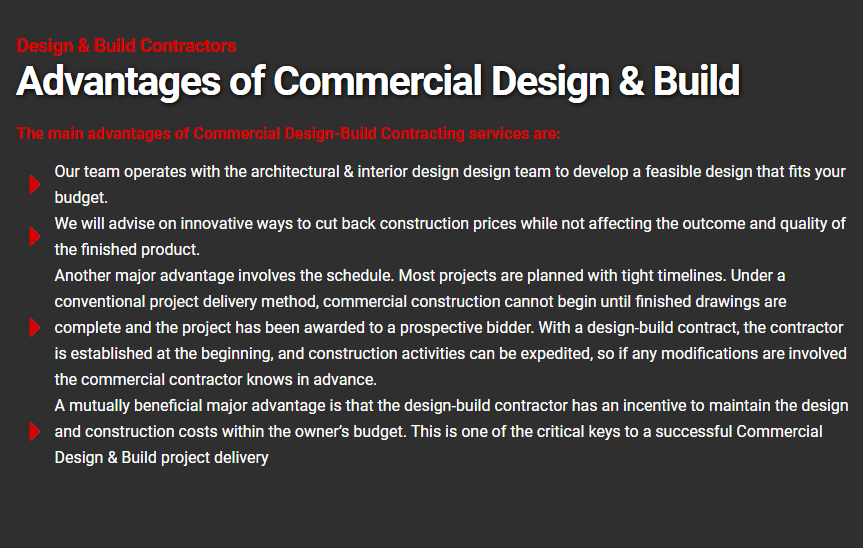
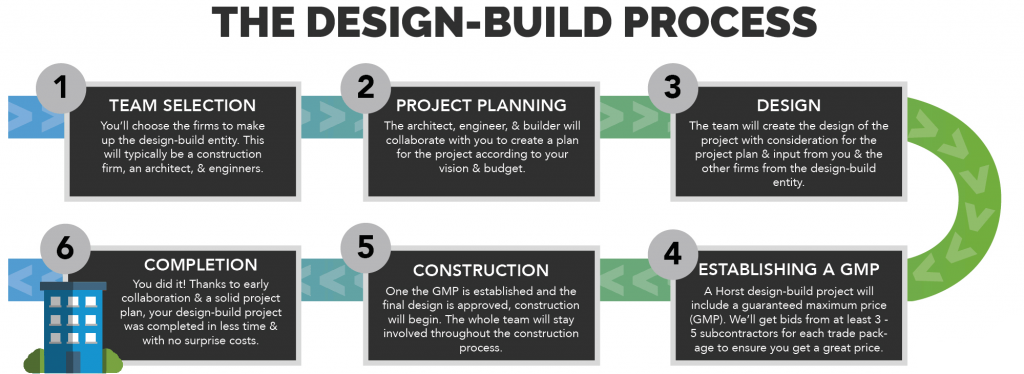
Each step in the process will typically include the following:
1. TEAM SELECTION
During the team selection phase, the owner will choose the firms that will make up their design-build team. This often includes the builder, architect, and engineers. Depending on the owner’s preference, they will either select one firm who will then choose the other members of the design-build team, or the owner will play an active role in the selection of all the firms that make up the team.
Regardless, these teams will band together contractually to form your design-build team. The success of the entire project will be their goal, as opposed to the success of just their area of expertise. This motivates them to work together from the start, looking at the big-picture success of the project.
2. PROJECT PLANNING
Once the design-build team is assembled, they’ll begin to plan out the project. They’ll match up your vision and goals for the project with your budget, and develop preliminary drawings, cost analyses, and schedules. They’ll analyze the project’s site and any existing structures or utilities located on the site, and they’ll look for potential challenges so they can prepare and plan accordingly.
3. DESIGN PHASE
Once the preliminary drawings fit into the rest of the project plan, the design phase begins. This is when the architect will complete the final drawings for the project. Unlike with the design-bid-build project approach, your project will benefit from having the input of the architect, builder, and any specialty subcontractors during this stage. This will lead to more accurate drawings, reducing the risk of constructability issues and change orders down the road.
4. ESTABLISHING A GMP
Next, the builder will assemble a more defined cost for the project. At Horst Construction, this includes at least three to five subcontractor bids for each trade package and a guaranteed maximum price (GMP).
A common concern with the design-build approach is that a project will cost more because the work won’t be competitively bid. However, that’s not the case. We make sure to get viable bids from a suitable amount of trusted, quality subcontractors, so you can be sure you’re getting a fair price.
In addition, your project will be secured with a GMP. A GMP is a set price for the project backed by the design-builder. It’s a promise that the project’s cost won’t go above that specific price. If it does, it’s the responsibility of the design-builder to pay—not the owner.
All Horst Construction design-build projects will put trade packages out to bid and include a GMP. But this won’t be the case with all design-build teams. We believe this is the best way to ensure the owner gets the fairest price for their project.
5. CONSTRUCTION
Once the design is finalized and the subcontractors and suppliers are selected, the project will begin construction. Because of the early collaboration on the part of the project team, the project should go relatively smoothly. The design-build approach has been shown to reduce or even eliminate the need for change orders and helps keep costs in line with the budget.
However, there is always the potential for unforeseen challenges to arise. But because the project rests on a solid plan from the beginning, the team will have more bandwidth to deal with challenges as they occur.
Once construction wraps up, the project will close out and the owner can move into their new building!